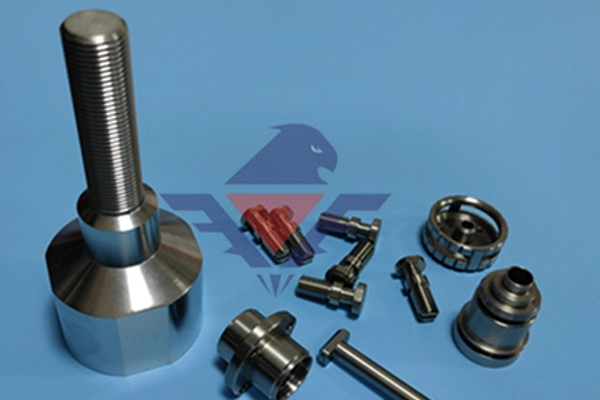
# Swiss Machining: Precision Engineering for Complex Components
## The Art of Swiss Machining
Swiss machining, also known as Swiss turning or Swiss screw machining, represents the pinnacle of precision manufacturing for small, complex components. Originating from Switzerland’s watchmaking industry in the late 19th century, this advanced machining technique has evolved to become indispensable across various high-tech sectors.
## How Swiss Machining Works
Unlike conventional lathes, Swiss-type machines feature a sliding headstock and guide bushing that provides exceptional support to the workpiece. This unique configuration allows for:
– Extreme precision with tolerances as tight as ±0.0001 inches
– Superior surface finishes
– Reduced vibration during machining
– Ability to machine long, slender parts without deflection
## Key Advantages of Swiss Machining
### 1. Unmatched Precision
The guide bushing system minimizes workpiece movement, enabling Swiss machines to achieve accuracies that conventional CNC machines struggle to match. This makes them ideal for medical implants, aerospace components, and electronic connectors.
### 2. Complex Geometries in Single Setup
Swiss machines can perform multiple operations simultaneously, including:
– Turning
– Milling
– Drilling
– Threading
– Grooving
This multi-tasking capability reduces production time and improves part consistency.
### 3. Material Efficiency
The Swiss machining process generates minimal waste, especially important when working with expensive materials like titanium or medical-grade alloys. The continuous feeding mechanism allows for optimal material usage.
## Industries That Rely on Swiss Machining
Several high-tech industries depend on Swiss machining for their most critical components:
– Medical: Surgical instruments, implants, and dental components
– Aerospace: Fuel system parts, hydraulic components, and fasteners
– Electronics: Connectors, pins, and miniature housings
– Automotive: Fuel injection parts and transmission components
– Defense: Precision munitions and firearm components
## Choosing the Right Swiss Machining Partner
When selecting a Swiss machining provider, consider these factors:
Keyword: Swiss Machining
– Experience with your specific industry requirements
– Quality certifications (ISO, AS9100, etc.)
– Material expertise
– Secondary processing capabilities
– Prototyping vs. production volume capacity
## The Future of Swiss Machining
As components continue to shrink while performance demands increase, Swiss machining technology evolves with:
– Advanced CNC controls
– Improved tooling materials
– Integration with automation systems
– Enhanced in-process measurement capabilities
This ensures Swiss machining remains at the forefront of precision manufacturing for years to come.